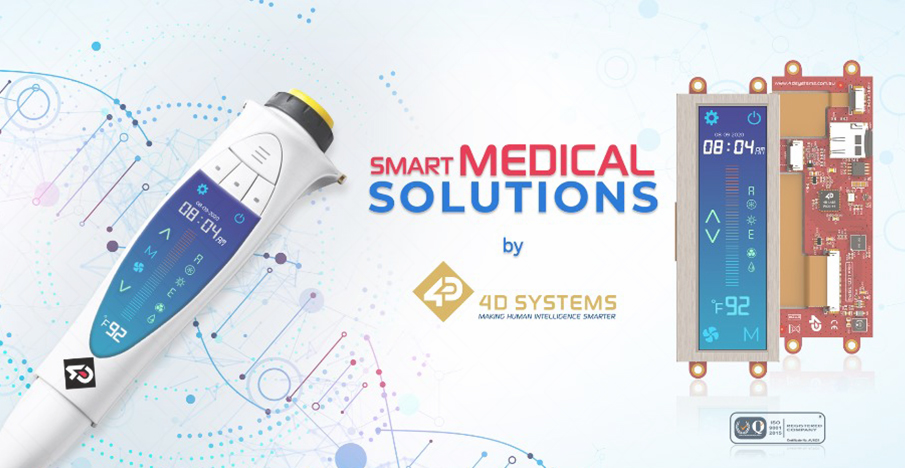
COVID-19 has forced businesses all over to rethink and realign themselves to the ‘new normal’.
What exactly this ‘new normal’ is, however, subject to continuous change. With vaccines now becoming available, businesses are gaining hope that they can see some normality return, however supply chains have been forever changed.
During the last year, many manufacturers around the world encountered lengthy delays as they waited on components to be delivered in order to finish production.
With so much dependency on the world’s key manufacturing countries, particularly China & Europe, businesses identified significant risks in their usual supply chains – product development teams had to urgently begin looking elsewhere in order to source high-quality parts that could be delivered within tight turnaround times.
Enter 4D SYSTEMS – a local Australian technology manufacturer, specialising in intelligent graphic solutions & embedded displays. To meet the demand, 4D SYSTEMS accelerated efforts to support the worldwide need for high-quality parts, particularly for the medical equipment manufacturing industry.
For example, the Portugal-based Centre of Engineering and Product Development, CEiiA, took decisive action to help build more ventilators to service hospitals worldwide in an effort to save as many lives as possible.
While the company primarily develops high-end technology solutions for the aeronautics, urban mobility and automotive sectors, their engineering team focused on building a highly-dependable medical device and required a graphic display solution that was “intuitive, easy to program, feature-rich and most importantly, reliable for the project”, as explained by CEiiA’s Director of the Product & Service Development Unit, Tiago Rebelo.
4D SYSTEMS supplied the solution CEiiA required – the ’gen4-uLCD-70DT Intelligent Display Module with Resistive-Touch, which was programmed using 4D SYSTEMS’ own feature-rich 4D WORKSHOP4 PRO IDE and ViSi Genie programming environment, and powered using its in house designed DIABLO16 processor.
The use of the gen4-uLCD-70DT led to CEiiA’s creation of the “Atena – an Invasive Medical Ventilator”, a medical device to provide mechanical invasive ventilation to patients, increasing the likelihood of survival from COVID-19.
Within just 45 days, CEiiA had produced a Medical Invasive Ventilator, featured in the CEiiA-produced video below. The ventilators were supplied to local and national hospitals and medical centers in Portugal.
Image: The Atena – Invasive Medical Ventilator by CEiiA
Image: 4D SYSTEMS’ gen4-uLCD-70DT in the Atena
As we can see in this example, Australia is playing an important role in providing technology products like microprocessors and embedded display touchscreens that form part of sophisticated medical equipment.
Quality matters every step of the way. Our hardware and software engineering teams are well seasoned, and work with ISO-9001 certified production factories using our own quality assurance procedures for impeccable outcomes.
The Australian government’s latest “Make it Happen: The Australian Government’s Modern Manufacturing Strategy” initiative is very promising, and 4D SYSTEMS, an ISO9001 and ISO14001-certified company, is well placed to contribute to display technology solutions manufactured in Australia related to some of the key priorities the government has identified: medical, space and resource technology.
For more information on how 4D SYSTEMS can offer smart display technology solutions, contact its Enterprise Solutions Centre.
Table of contents
Subscribe to our newsletter
Latest Case Studies
This case study unveils a practical application of embedded innovation, highlighting the process and outcomes of upgrading legacy systems in a technology-focused product line. Through strategic technological integration, the project not only uplifted product performance but also markedly improved customer satisfaction levels. The subsequent pages delve into various strategic and operational enhancements made, providing readers with a nuanced understanding of the concrete impacts and subtleties involved in a real-world, engineer-led embedded innovation initiative. A testament to blending traditional systems with modern innovation.
Duratec, specializing in liquid handling devices for various industries, aimed to simplify the control interfaces of their new product line. Partnering with 4D Systems, they integrated a touch display module enhancing user-centricity and operational efficiency. This transition replaced outdated control panels with an intuitive, modern interface without compromising on control capabilities via the RS232 interface. Three new devices were launched, improving user interactions through user-friendly touch displays, showcasing Duratec's commitment to innovation. This collaboration allowed for more straightforward control, monitoring, and interaction with Duratec's devices, ensuring a better user experience and meeting industry demands.
In the challenging process of creating an advanced 3D printer, BCN3D encountered an unexpected difficulty: finding an appropriate, user-friendly display module. Despite initial struggles, BCN3D discovered the solution in 4D Systems’ gen4 display modules. These modules offered superior resolution, processing power, and flexibility. Key to BCN3D's decision was the modules' easy integration via a serial connection and the Arduino-compatible library into their firmware. For its Sigma R17 3D printer, BCN3D upgraded to the gen4-ULCD-35DCT-CLB, a 3.5-inch Intelligent TFT-LCD display module with capacitive touch, further enhancing the user experience. The gen4 series of intelligent display modules perfectly matched BCN3D's requirements, offering innovative solutions in the sophisticated 3D printing space.